Najdôležitejším článkom určujúcim spôsob odlievania ocele pri ZPO je kryštalizátor. Práve toto zariadenie primárne určuje kvalitu odliatku a aj všetky ostatné parametre a zariadenia sa mu prispôsobujú. Od prvých patentov určoval smer liatia a nastavenie uhla sekundárneho chladenia.
Rozoznávame 4 hlavné typy ZPO:
1, vertikálne
2, horizontálne
3, so zakrivením
4, špeciálne
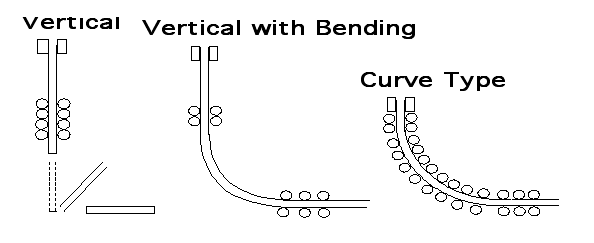
Rozdelenie typov ZPO vertikálne a s možnosťou zakrivenia
1, Vertikálne ZPO je historicky prvým zariadením skonštruovaným anglickým inžinierom B. Athom podľa patentu podaného v roku 1886. Skladalo sa z medzipanvy, zvislého vodou chladeného kryštalizátora, ťažných valcov. Následné vylepšenia tohto patentu prinášali zásadné zmeny v kvalite vyrábaných odliatkov. Stroj z roku 1887 už mal zabudované priame chladenie predliatku medzi valcami a rezanie predliatku počas odlievania. Stále však pretrvávali problémy s nalepovaním stuhnutej kôry predliatku o steny kryštalizátora. Tento problém riešil nemec D. Junghaus aplikáciou oscilačného kmitania kryštalizátora v roku 1933, ktoré bolo navrhnuté Petersonom v r. 1916. Predliatky začali vykazovať oveľa kvalitnejší povrch. Ďalším zdokonalením oscilácie kryštalizátora navrhol Holliday, a to tým, že sa pohyb vpred a späť dial rôznou rýchlosťou. Smerom dole je rýchlosť vyššia ako vyťahovanie predliatku z kryštalizátora, a tým vzniká tzv. negatívne stripovanie. V smere nahor je rýchlosť asi trikrát vyššia ako smerom dole. Z toho vznikli dve zásadné konštatovania:
a, kryštalizátor sa nesmie nikdy pohybovať rovnakou rýchlosťou ako predliatok.
b, tlak kryštalizátora smerom dole na kôru predliatku pôsobí priaznivo na prevenciu proti prievalom.
Prednosti vertikálneho plynulého odlievania spočívajú v:
1, dokonale symetrické pomery liatia a tuhnutia
2, jednoduché vedenie priameho predliatku
Nevýhodami tohto spôsobu sú:
1, veľká výška ZPO
2, ohraničenie maximálnej dĺžky predliatku výškou ZPO
2, Horizontálne ZPO bolo uvedené do prevádzky prvýkrát vo firme General Motors v Lansing Michigan USA v roku 1969. Hlavnými výhodami HZPO sú:
- nízke investičné náklady
- vysoká prispôsobivosť prevádzkovým podmienkam
- skrátený a zjednodušený tok materiálu
- jednoduchá obsluha a ľahký prístup k jednotlivým uzlom zariadenia
- zjednodušená údržba a demontáž
- nižšia spotreba materiálov a energie
- nižšia výška a hmotnosť zariadenia
Na tomto zariadení šiel vývoj najprv oscilujúcim kryštalizátorom pevne spojeným s medzipanvou a konštantnou rýchlosťou ťažných valcov, potom oscilujúceho kryštalizátora bez medzipanvy a nakoniec s oscilujúcim predliatkom. Najdoležitejším uzlom HZPO je odtrhávací krúžok. Je to medzičlánok pred vstupom ocele do kryštalizátora. V ňom začína tvorba kôry predliatku, preto je dôležité, aby odtrhávací krúžok spĺňal všetky potrebné požiadavky pre dobrú kvalitu povrchu predliatkov. Hlavná je tesnosť krúžka s kryštalizátorom, čiže rozmerová presnosť, pevnosť materiálu, teplotná odolnosť. Odtrhávacie krúžky sa vyrábajú z nitridu kremíka, nitridu bóru a sialonu ( Si5AlON7).
3, ZPO s uhlom zakrivenia je zariadením, na ktorom sa pomocou ohýbacích valčekov predliatok ohýba pod daným uhlovým stupňom. Ohyb prebieha v čiastočne stuhnutom predliatku, pred tzv. bodom červeného žiaru. Po ohybe je rovnaný rovnacou stolicou s valcami.
Pre ešte väčšie zníženie výšky zariadenia bolo skonštruované radiálne ZPO so zakriveným kryštalizátorom. Týmto konštrukčným zásahom sa znížila výška ZPO o 50%. Pribudli však problémy s asymetriou odlievaného predliatku v zakrivenom oscilujúcom kryštalizátore, ktoré sa riešili zavedením technológie ponorného liatia a liacimi práškami. Tento typ sa vyznačuje jednoduchosťou a hospodárnosťou:
- nie je potreba stavania vysokých hál
- ťažná a rovnacia stolica sú spoločne uložené
- je možné odliať aj veľmi dlhý odliatok
Polomer ohybu sa počíta:
Pri úplnom stuhnutí R = 26 až 32 D
Pri čiastočnom stuhnutí R = 32 až 40 D , D je hrúbka ohybaného predliatku.
Inou možnosťou radiálneho ZPO je zariadenie s vertikálnym rovným kryštalizátorom a následným zvislým ťahaním predliatku a ohnutým sekundárnym chladením.
4, Špeciálne druhy ZPO majú za úlohu odlievať poloprodukty tvarovo veľmi blízke konečným výrobkom s minimálnou možnou mierou opracovávania, valcovania a tvarovania. Jedným z týchto známych spôsobov je aj liaci stroj Hazelett.

odlievací stroj Hazelett
Tento stroj tvorí medzipanva a kryštalizátor z dvoch paralelne sa pohybujúcich oceľových pásov nepretržite chladených vodou. Na okrajoch medzi pásmi sa nachádzajú bočné steny, s ktorými je možné manipulovať a tým meniť rozmer produktu. Výhodou je vysoká akosť povrchu, energetická nenáročnosť, vysoký výkon, okamžitá a plynulá zmena šírky a aj hrúbky produktu, s možnosťou odlievania štvorcových prierezov a to doplnením prepážok na pásy. Merania naznačujú, že je možné odliať 300 t ocele za hodinu, pri hrúbke bramy 150 mm a šírke 1500 mm. Rýchlosť liatia sa pohybuje okolo 9 až 24 m za minútu. Od roku 1965 tento stroj využíva spoločnosť Bethlehem steel v USA.
video o Bethlehem Steel (pozor má cez hodinu :))
Ďalšími špeciálnymi spôsobmi sú napr. RCC proces a metóda BSC, kde kryštalizátorom je rad ťahaných liacich vozov a tiež liaci stroj firmy LTV, pre liatie tenkých oceľových pásov. Menované zariadenia sú schematicky zobrazené:
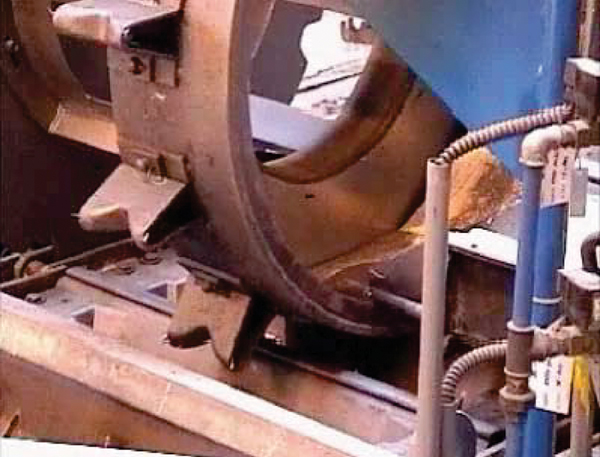
obr. RCC systém
1 – predliatok 2 – medzipanva 3 – pás
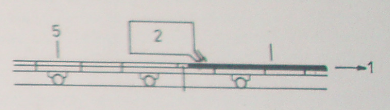
obr. Liaci systém BSC
1 – predliatok, 2 – medzipanva, 3 – pás, 4 – bočné steny z kovových blokov, 5 – liaci voz

obr. Liaci stroj LVT
1 – vtoková časť, 2 – oceľový predliatok, 3 – vnútorný liaci bubon, 4 – vodné trisky 5 – vnútorný liaci krúžok
Druhým deliacim parametrom je tvar konečného odliatku, ktorý sa samozrejme vyformuje v kryštalizátore, vytvorením a stuhnutím kôry po jeho stenách. Dajú sa tu rozlíšiť tieto špecifické tvary:
1, blok
2, sochor
3, brama
4, špeciálne profilové tvary
5, tenké predliatky blízke hotovým produktom
Ďalším parametrom rozlišovania ZPO je založený na počte prúdov, teda na počte kryštalizátorov, ku ktorým je prispôsobená medzipanva s požadujúcim počtom výtokov. Počet prúdov je určený množstvom vyrobenej ocele, teda koľko ton ocele potrebujeme odliať na jednu tavbu a tiež rozmermi odlievaného odliatku. Rozlišujeme tu tieto možnosti:
1, dvojprúdové
2, štvorprúdové
3, osemprúdové
4, špeciálne
Dvojprúdové ZPO sa využíva hlavne pri liatí brám. Príkladom dvojprúdového ZPO je USS Košice. Štvorprúdové ZPO je využívané na liatie sochorov a blokov. Príklad ŽP a.s. v Podbrezovej. Osemprúdové ZPO s jednou medzipanvou sa využíva pri liatí sochorov a s dvoma medzipanvami pre liatie blokov. Využiteľné je najmä vo veľkých oceliarňach, kde sa nachádza viac ako 1 agregát pre výrobu surovej ocele. Špeciálnymi možnosťami sa rozumie väčšinou kombinácia rôznych tvarov kryštalizátora.
Typy kontinuálne odlievaných ocelí:
- Uhlíkové – ULC, ELC, IF
- Uhlíkové – hlbokoťažné /kohaly, obaly - LCAK/
- Uhlíkové – peritektické /konštrukčné/
- Uhlíkové – so stredným obsahom C
- Uhlíkové – s vysokým obsahom C
- Mikrolegované /HSLA, KX/
- Ocele pre elektrotechniku /Dynamo, Trafo/
- Antikorózne ocele
- Rýchlorezné ocele
- Martenzitické ocele
- Poloukľudnené ocele
obr. Rozdelenie uhlíkových ocelí
Nízkouhlíkové ocele obvyklých akostí, konštrukčné, LC, ULC, alebo mikrolegované tvoria najväčšiu skupinu konštrukčných materiálov s veľkým významom pre viaceré odvetvia priemyslu. V súčasnosti sa takmer výhradne vyrábajú technológiou plynulého odlievania.
Hlavný dôvod, prečo sa dnes mnohé konštrukčné ocele vyrábajú s obsahom Cmax = 0,10 % je, že v nich neprebieha peritektická kryštalizácia. Ich veľmi časté praskanie je problém, ktorý spočíva nielen v samotnej peritektickej reakcii, ale aj v objemových zmenách a v zmenách v rozpustnosti nečistôt, ktoré ju sprevádzajú.
Porovnaním reakcií tuhnutia pri rôznom percentuálnom zastúpení C sa dá rozoznať päť typov ocelí:
I. typ C < 0,1% : L→ L+δ → δ→ γ
II. typ 0,1 < C < 0,18%: L→ L+δ → L+ δ+ γ→ δ+ γ → γ
III. typ C = 0,18%: L→ L+δ → L+ δ+ γ→ γ
IV. typ 0,18 < C < 0,52%: L→ L+δ → L+ δ+ γ→ L+ γ→ γ
V. typ C > 0,52%: L→ L+ γ→ γ
Z analýzy autorov vyplýva, že najdôležitejšími pozorovanými faktormi vplývajúcimi na praskanie peritektických ocelí pri plynulom odlievaní sú: tvorba hrubého austenitického zrna, precipitácia sulfidov a oxisulfidov na hraniciach dendridov alebo hraniciach austenitických zŕn a nemenej dôležité makroskopické napätia, vyvolané objemovými zmenami pri tuhnutí.
Operácie pred plynulým odlievaním ocele:
- Kontrola kryštalizátora
- Príprava a úprava ďalších uzlov
- Príprava štartovacej tyče
- Príprava medzipánvy k odlievaniu
- Zabudovanie výleviek
- Príprava zátkovej tyče
- Upevnenie ponorných liacích trubíc
- Nastavenie medzipánvy do liacej polohy
- Príprava spotrebného materiálu
- Pristavenie liacej pánvy