Terciálna metalurgia sa delí na:
1, medzipanvovú
2, kryštalizátorovú
Toto delenie je dôležité z hľadiska rozčlenenia operácií v daných úsekoch a možnosti eliminácie vnútorných a povrchových vád. Pre medzipanvové operácie platí, že môžu ovplyvniť kvalitu ocele tesne pred jej odliatím. Preto sa do vývoja medzipanvovej metalurgie investovalo kvantum času a finančných prostriedkov.
Medzipanva spĺňa na ZPO tieto metalurgické funkcie:
- je zásobáreň tekutej ocele pred odliatím a počas výmeny liacej panvy
- je transportér ocele pre jednotlivé liace prúdy
- minimalizuje rozstrek liaceho prúdu
- znižuje ferostatický tlak ocele
- homogenizuje tekutú oceľ chemicky a tepelne
- oddeľuje oceľ od trosky
- vyhodnocuje sa v nej rýchlosť liatia prostredníctvom meranej teploty
- zrovnomerňuje rýchlosti pri odlievaní
- udržuje stabilný konštantný tok ocele
- udržuje stálu výšku hladiny v kryštalizátore
- dekantujú sa v nej nekovové inklúzie
- je možné v nej uplatniť posledné metalurgické operácie ako legovanie a dezoxidácia
- riadením prúdenia znižuje retenčný čas a tiež znižuje mŕtve objemy
- minimalizuje možnosť turbulentných zón v liacom prúde
- separuje nečistôty prostredníctvom rafinačnej trosky
Pre splnenie všetkých očakávaných výhod medzipanvovej metalurgie je prvotne dôležitou otázka konštrukcie medzipanvy. Podľa vyrábaných predliatkov sa medzipanvy delia na:
1, sochorové,
2, blokové
3, bramové
4, kombinované ( sochorové & blokové & bramové)
5, pre odlievanie tenkých profilov (near net shape casting, thin slab casting)
5, pre odlievanie tenkých pásov (strip casting)
Delenie medzipanvy podľa typu ZPO :
1, pre vertikálne a radiálne ZPO
2, pre horizontálne ZPO
3, pre špeciálne druhy odlievania
Delenie medzipanvy podľa počtu prúdov:
1, 1 – 2 prúdové ( odlievanie brám)
2, 3 – 5 prúdové (odlievanie blokov, sochorov)
3, 6 prúdové (odlievanie sochorov, tzv. psích kostí – beam blank)
4, 8 prúdové ( odlievanie blokov, sochorov; sú to 2 medzipanvy, 2x4 prúdy )
Delenie medzipanvy podľa tvaru:
1, Obdĺžníkový tvar
2, Klínovitý tvar
3, Trapezoidný (delta tvar)
4, T tvar
5, C tvar
6, H tvar
7, L tvar
8, Kruhový tvar
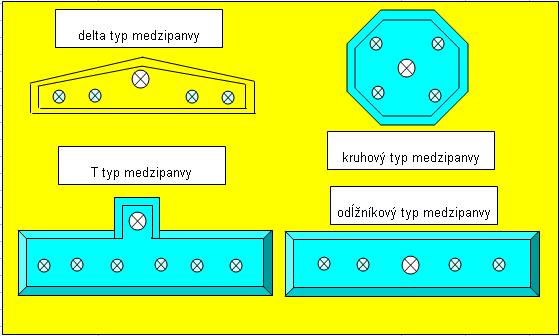
Delenie medzipanvy podľa symetrie vtokovej a výtokovej sústavy:
1, symetrický (USS Košice s.r.o.)
2, asymetrický (ŽP a.s., Třinec a.s.)
Delenie medzipanvy podľa objemu:
1, malá – do 20 ton (ŽP a.s.)
2, stredná – sú od 20 do 40 ton
3, veľká – nad 40 ton ocele
Konštrukcia medzipanvy
Medzipanva je zozváraná z oceľových plechov s výstužnými rebrami a vybavená žiaruvzdornou výmurovkou. V dne medzipanvy sú zamurované výtokové otvory. Špeciálnymi doplnkami medzipanvy sú podľa potreby umiestnené hrádzky, prepážky, dopadová doska, tvárnice pre prefúkavanie inertným plynom. Všetky doplnky, vzdialenosti výtokových uzlov a tvar a veľkosť medzipanvy je daný konštrukciou celkového ZPO. Na medzipanvu sa môže, ale nemusí umiestniť veko.
nacvičte si konštrukciu medzipanvy klikom na obr.
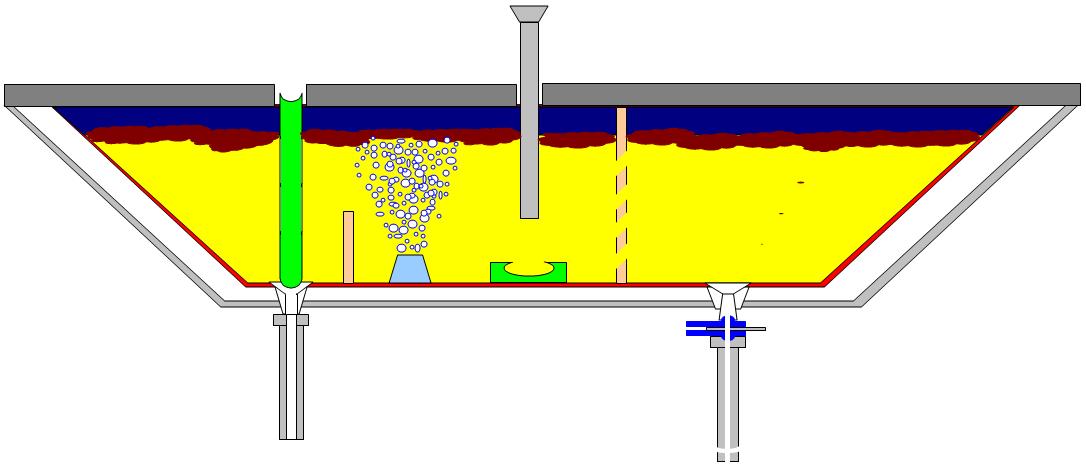
Žiaruvzdorné materiály používané v MP
Žiaruvzdorná výmurovka medzipanvy slúži hlavne na udržiavanie teploty tekutej ocele v medzipanve pri súčastnom zachovaní dostatočnej odolnosti proti korózii a ochranu oceľovej konštrukcie medzipanvy. Výmurovka medzipanvy sa pred použitím môže predohrievať na teplotu 1100 - 1500 °C, vtedy ide o teplú výmurovku, alebo sa nemusí, ak ide o studenú výmurovku. V medzipanvách sa používajú trojvrstvové výmurovky izolačná, trvalá a pracovná.
Podľa spôsobu vymurovania rozlišujeme výmurovky:
- murované zo žiaruvzdorných tvaroviek
- monolitické : dúsané, liate, torkrétované, vymazávané
- kombinované
Prvou vrstvou výmurovky nanášanej na oceľový plášť medzipanvy je izolačná výmurovka. Pozostáva z hlinitokremičitanových izolačných žiaruvzdorov o hrúbke 10 – 20 mm. Druhou vrstvou je trvalá výmurovka, kde sú použité hlinitokremičitanové žiarobetóny. Jej hrúbka závisí od tvaru medzipanvy, na dne je oveľa hrubšia. Pracovná časť výmurovky medzipanvy sa zhotovuje z tepelnoizolačnej magnéziovej zmesi, ktorá je nastrekovaná v 2 – 3 centimetrovej vrstve na trvalú výmurovku, ktorá sa obnovuje po každej sekvencii. Hrúbka závisí od počtu tavieb. Ľahké oddelenie trvalej a pracovnej výmurovky je spôsobené rozdielnym koeficientom teplotnej roztiažnosti oboch materiálov, na základe ktorej vznikajú trhliny na styku oboch vrstiev.
Najerózivnejšou zónou medzipanvy je miesto dopadu prítoku ocele z liacej panvy. Na toto miesto sa špeciálne umiestňujú dopadové dosky alebo tvarovky – turbostopy. Materiál pre špeciálnu keramiku vo vtokovej zóne má vysoké termomechanické parametre. Používajú sa materiály bázické s priamou väzbou, mullitokorundové a korundové žiarobetóny. Pre ohraničenie tejto zóny od výtokových zón medzipanvy sa používajú prepážky. V tejto zóne sa hromadí zásypový piesok, strhnutá troska z liacej panvy a najviac nečistôt prichádzajúcich s oceľou, ktoré sa následne kumulujú v krycej troske, preto je dôležité túto časť trosky pravidelne sťahovať a pridávať novú.
Prepážky môžu byť vymurované z magnezitových tehál, alebo môžu byť monolitické. Výhodnejšie sú monolitické, keďže menej erodujú a nerozpadajú sa, a tým plnia aj ďalšiu funkciu v medzipanve ako usmerňovače prúdu a filtre tekutej ocele.
Podobne sú do dna medzipanvy vsadené aj monolitové hrádzky a stavidlá. Slúžia na usmerňovanie prúdenia v medzipanve, na zabránenie vytvárania nechcených prúdov. V dne môže byť zabudovaná aj porézna tvárnica pre prefúkavanie taveniny inertným plynom na lepšie odstraňovanie nekovových inklúzií.
Usporiadanie mechanických deflektorov v MP
Správnou konštrukciou medzipanvy sa rozumie optimálne rozmiestnenie prepážok a dopadovej dosky, vzhľadom na vypočítané a namodelované hodnoty retenčného času, smerov prúdenia taveniny, vplyvu objemu, turbulencie atď. Výsledná kvalita ocele závisí na možnosti, čo najmenšieho strhávania trosky a maximálneho vyplavovania nekovových vtrúsenín, a preto je potrebné dosiahnuť v medzipanve laminárny prúd namiesto turbulentného. Paradoxne ale turbulentné prúdenie v MP zabezpečuje prenos hmoty a teploty v tekutej oceli a teda homogenizáciu taveniny. Iný problém - neprietočné objemy môžu viesť k tepelným stratám a vytváraniu zhlukov pri výtokových uzloch a následne ich zalepovaniu. Preto prietok v MP musíme viesť optimálnym riadením smerov prúdu a teplotných gradientov.
Mechanické usmerňovače (turbostop, dopadová doska, prepážky, hrádzky, atd.) majú riadiť dynamiku prúdenia kvôli:
- zaisteniu dostatočného priemerného retenčného času
-
zaisteniu čo najmenšieho rozptylu retenčného času pre jednotlivé výlevky medzipanvy
-
minimálnemu objemu mŕtvych zón (neprietočných objemov)
-
zaisteniu prúdenia smerom k povrchu taveniny
-
zaisteniu maximálneho priestoru pre laminárne prúdenie taveniny
- minimalizáciu turbulentného miešania
Retenčným časom rozumieme dobu zotrvania prietokového elementu v medzipanve od okamihu napustenia až po výtok do kryštalizátora, ktorý závisí od:
- rýchlosti liatia
- výšky hladiny tekutej ocele v MP
- spôsobu vtoku ocele do MP
- spôsobu výtoku ocele z MP
- injektáže inertného plynu v priestore MP
- injektáže inertného plynu do prúdu ocele pri výstupe z MP
Retenčný čas priaznivo ovplyvňuje vyplavovanie nekovových nežiadúcich prímesí z objemu tekutého kovu a je závislý na objemovej veľkosti medzipanvy a tiež na vzdialenosti a umiestnení výtokovych otvrov.
Mŕtvy objem (neprietočný) Vd sa posudzuje ako objem taveniny v medzipanve, ktorý zotrváva v relatívnom kľude po dobu dlhšiu než je dvojnásobok retenčného času. Tento jav sa snažíme eliminovať do maximálnej miery hlavne kvôli zamedzeniu havarijných stavov, ktoré vznikajú pri tzv. zmrznutí tavby, čo znamená, že teplota tekutej ocele klesne pod úroveň 10 °C nad teplotu liquidu.
Tteplota liquidu TLiq je vypočítaná číselná hodnota v °C pre konkrétne zloženie ocele, pri ktorej dochádza k premene taveniny na tuhý stav. Vypočítava sa podľa vzorca:
TLiq ___.= 1536 – [78.(%C) + 7,6.(%Si) + 4,9.(%Mn) + 34.(%P) +
+ 30.(%S)+ 5,0.(%Cu) + 3,1.(%Ni) + 1,3.(%Cr)+
+3,6.(%Al) + 2,0.(%Mo) + 2,0.(%V) + 18.(%Ti)] [°C]
Opačným momentom ako zmrznutie tavby je prehriatie ocele "SUPERHEAT". Ak má tekutá oceľ zvýšenú teplotu oproti teplote liquidu do 50 °C, považuje sa to za hodnotu v tolerancii. Pri teplotách vyšších ako 50°C už hrozí riziko, že takto prehriatu oceľ nestihne kryštalizátor dostatočne ochladiť a vytvoriť na jej povrchu dostatočne hrubú liacu kôru, čo následne môže viesť k pretrhnutiu kôry a prievalu. Odlievacia teplota je teplotný interval medzi telotou zmrznutia ocele a prehriatia. Odlievacia teplota je preto veľmi dôležitým parametrom, ktorý určuje aj ďalšie nastavenia systému odlievania na ZPO, napr. presne podľa odlievacej teploty je nastavená rýchlosť liatia (o nej bližšie v stati sekundárne chladenie). Výpočet odlievacej teploty si skúste tu.
V medzipanve sa okrem mŕtveho objemu, ktorý sme si popísali, nachádzajú objemy v pohybe. Rozdeľujeme ich podľa toho akým spôsobom sa tieto prúdy pohybujú na:
1, objem s laminárnym tokom Vp
2, objem s turbulentným tokom Vm
1, Laminárny tok je dôležité zabezpečiť hlavne v časti medzipanvy pod troskou. tým dosiahneme primerané podmienky pre vyplavovanie nekovových inklúzií, ich rafináciu troskou a nestrhávanie trosky do objemu ocele.
2, Turbulencia v prúdení tekutej ocele nepriaznivo pôsobí na čistotu ocele tým, že obmedzuje vyplavovanie nekovových iklúzií a svojím pohybom spôsobuje strhávanie časti trosky nad kovovým kúpeľom. Naproti tomu spôsobuje aj tepelnú a chemickú homogenizáciu roztaveného kovu.
Tieto prúdenia sa v medzipanve nachádzajú pri stabilnom režime odlievania. To znamená, že medzipanva je naplnená tekutou oceľou na maximálnu hmotnosť. Pri výmene liacej panvy, sa ale prítok tekutého kovu odstrihne a medzipanva sa dostáva do režimu prechodového (tranzitného), ktorý je spojený s poklesom hladiny taveniny v medzipanve. Optimalizované prúdenie sa začne meniť, čo má dosah na vyplavovanie inklúzií, strhávanie trosky a celkovú čistotu ocele. S poklesom hladiny sa troska nalepuje po stenách medzipanvy a môže dochádzať k odkrývaniu kovové kúpeľa a interakciám medzi oceľou, troskou a okolitou atmosférou, či už pôsobením nalepovania sa trosky o steny, alebo vírivým prúdom rozháňajúcim trosku do strán. Po otvorení liata ďalšej medzipanvy sa výška hladiny vráti do pôvodnú úroveň. Troska, ktorá ostala nalepená na stenách, sa ľahko dostáva do ocele a znečisťuje ju.
Troska
V medzipanve sa tekutá oceľ chráni pred reoxidáciou a naplynením medzipanvovou troskou, ktorá vzniká roztavením rafinačného a krycieho prášku. Jej najdôležitejším pásmom medzi jednotlivými zónami je jej rozhranie s tekutým kovom, kde zabezpečuje pohlcovanie nekovových inklúzií . Trosky sú mnohozložkové, v prevažnej miere oxidické taveniny v bezprostrednom kontakte s kovom, pričom plnia dôležité technologické funkcie. Zloženie trosky a nadväzne aj jej aktivita, teplotné charakteristiky tavenia, viskozita, povrchové napätie ako i ďalšie charakteristiky vo významnej miere určujú kvalitu vyrábanej ocele.
Chemické zloženie krycej trosky môže byť napríklad na báze týchto oxidov: CaO, SiO2, Al2O3, Cr2O3, TiO2, MnO, MgO, K2O, Na2O, k nim sa pridávajú riedidlá kazivec, sóda, Na3AlF6 a C vo forme grafitu v množstve 3 – 40% hmotnosti trosky. Bazicita medzipanvovej trosky je nízka, pohybuje sa v rozmedzí 0,01 – 1,5.
Rafinačná troska sa nachádza pod krycou a má za úlohu zabezpečovať pohlcovanie nekovových inklúzií a zabraňovať sekundárnej oxidácii. Tieto trosky sú v tekutom stave a ich zloženie môže byť nasledovné: 44,5 % Al2O3, 42% CaO, 4% SiO2, 1,5% MgO, 1% Fe2O3, 1,5% MnO, 1% Na2O, 1,4% K2O a 1,4% C.
Výtok ocele z medzipanvy je zabezpečený požadovaným počtom výtokových uzlov.
K výtokovému uzlu medzipanvy patrí výtokový kameň, výlevka, uzatvárací systém medzipanvy a ponorná trubica. Existuje celá rada variant aplikácie týchto dielčích častí.
V súčasnej dobe sa pri vyústení z medzipanvy používajú ako zátkové tak aj šupátkové uzávery. Slúžia na reguláciu liaceho prietoku ocele z medzipanvy do kryštalizátora. Hlavné rozdiely sú v tom, že šupátkový uzáver je investične približne 10 krát drahší ako zátkový, cena žiaruvzdorného materiálu je približne 5 krát vyššia a vyžaduje vyššiu liacu teplotu o 10 až 15 °C. Naproti tomu iné štúdie ukazujú, že náklady na žiaruvzdorný materiál možno znížiť o 40 % tým, že sa skráti príprava medzipanvy k ďalšiemu liatiu.
Šupátkový uzáver
Rozhodujúcou pre trvanlivosť šupátkových uzáverov je kvalita keramických dosiek. Dosky šupátkových uzáverov majú mať vysokú pevnosť v ohybe pri vyššej teplote, vysokú tepelnú vodivosť, nízku teplotnú rozťažnosť, nízku pórovitosť a malé póry, dobrú opracovateľnosť s dôrazom na vysokú kvalitu povrchu a vysokú odolnosť proti erozívnemu pôsobeniu tekutého kovu.
Dosky sa vyrábajú na báze Al2O3, MgO, ZrO2 . Sú doporučené trojdoskové systémy, ktorých parametre ako priemer výtokového otvoru a posun strednej dosky sú odvodené od typu odlievaných odliatkov (bramové, blokové, sochorové). Horizontálne medzery medzi hornou doskou a výlevkou i medzi dolnou doskou a ponornou trubicou je dôležité tesniť proti vnikaniu tekutej ocele. Medzery sa tesnia vysokožiaruvzdornými tmelmi, napr. na báze korundu s prídavkom oxidu zirkoničitého.
Pre pokrytie povrchu šúpatkových dosiek sa tiež využíva korundový materiál s uhlíkovou väzbou, lebo majú o 30 % vyššiu životnosť. Korundový materiál s uhlíkovou väzbou môže pozostávať napr. zo 77 % Al2O3, 8 % SiO2, 12 % C, má objemovú hmotnosť 2850 kg.m-3, pórovitosť 2,1 %. Amorfný uhlík sa veľmi ťažko rozpúšťa v tekutej oceli, ktorá dosky prakticky nezmáča. Materiál má jemnozrnnú štruktúru s veľmi malými priemermi pórov. 90 % pórov je menších ako 1 µm.
Monobloková zátka
Monoblokové zátky sa vyrábajú z materiálov na báze Al2O3, MgO, ZrO2, a to s uhlíkovou väzbou. Štúdie poukazujú na značné opotrebenie zirkoničitých materálov vyrobených z ZrO2 stabilizovaného CaO alebo MgO. Takto stabilizovaný oxid zirkoničitý je v redukčnej atmosfére atakovaný prvkami Al, Fe, Si a tiež ich oxidmi. Al2O3 a SiO2 rozpúšťajú stabilizačné komponenty ZrO2, pričom vytvárajú nízkotaviteľné fázy, ako napr. anortit – Ca (Al2Si2O8). Tvoria sa jemné čiastočky ZrO2, ktoré sú oceľou ľahko odplavované.
Materiály MgO sú stabilnejšie, keďže existuje len jedna jeho modifikácia - kubická. Reakcie s SiO2, Al2O3 a MnO sú veľmi pomalé a výsledné produkty majú prevažne vysokú žiaruvzdornosť, ako napr. forsterit – Mg2SiO4.
Pri predohreve výtokového uzla môže u materiálov s uhlíkovou väzbou vyhorievať uhlík a oduhličená vrstva potom neodoláva erozívnemu pôsobeniu ocele. Preto sa žiaruvzdorná vrstva natiera glazúrou, ktorá vytvára na povrchu nerozpustnú vrstvu.
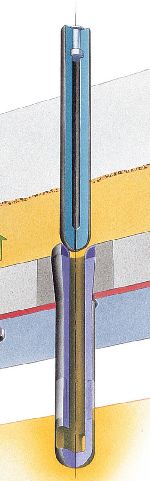
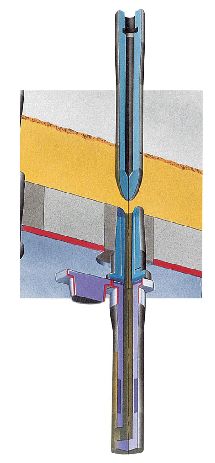

Obr. Typy monoblokových zátok
kliknutím na obr. spustíte simuláciu
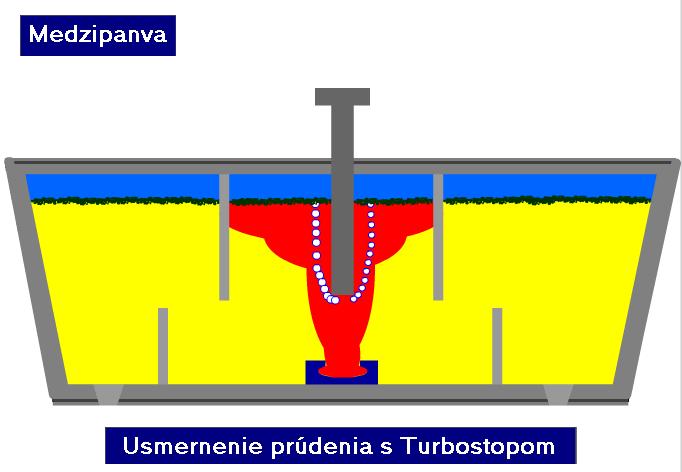